Understanding the Fundamentals and Applications of Plastic Extrusion in Modern Production
In the realm of modern-day production, the method of plastic extrusion plays an instrumental function. Untangling the fundamentals of this process exposes the real adaptability and possibility of plastic extrusion.
The Fundamentals of Plastic Extrusion Refine
While it may appear complex, the fundamentals of the plastic extrusion procedure are based upon relatively uncomplicated concepts. It is a production process in which plastic is melted and after that formed into a continuous profile through a die. The raw plastic material, often in the kind of pellets, is fed into an extruder. Inside the extruder, the plastic is subjected to warm and stress, causing it to melt. The molten plastic is after that compelled via a shaped opening, referred to as a die, to form a long, continual item. The extruded item is cooled down and afterwards cut to the desired size. The plastic extrusion procedure is extensively utilized in various industries due to its effectiveness, cost-effectiveness, and versatility.
Different Kinds Of Plastic Extrusion Strategies
Building upon the standard understanding of the plastic extrusion procedure, it is required to explore the various strategies associated with this manufacturing method. The two key techniques are profile extrusion and sheet extrusion. In profile extrusion, plastic is melted and formed into a constant profile, often used to produce pipes, poles, rails, and home window structures. In comparison, sheet extrusion creates huge, level sheets of plastic, which are normally additional refined right into products such as food product packaging, shower drapes, and auto parts. Each strategy needs specialized equipment and accurate control over temperature and pressure to guarantee the plastic keeps its shape during cooling. Understanding these strategies is crucial to using plastic extrusion successfully in contemporary production.
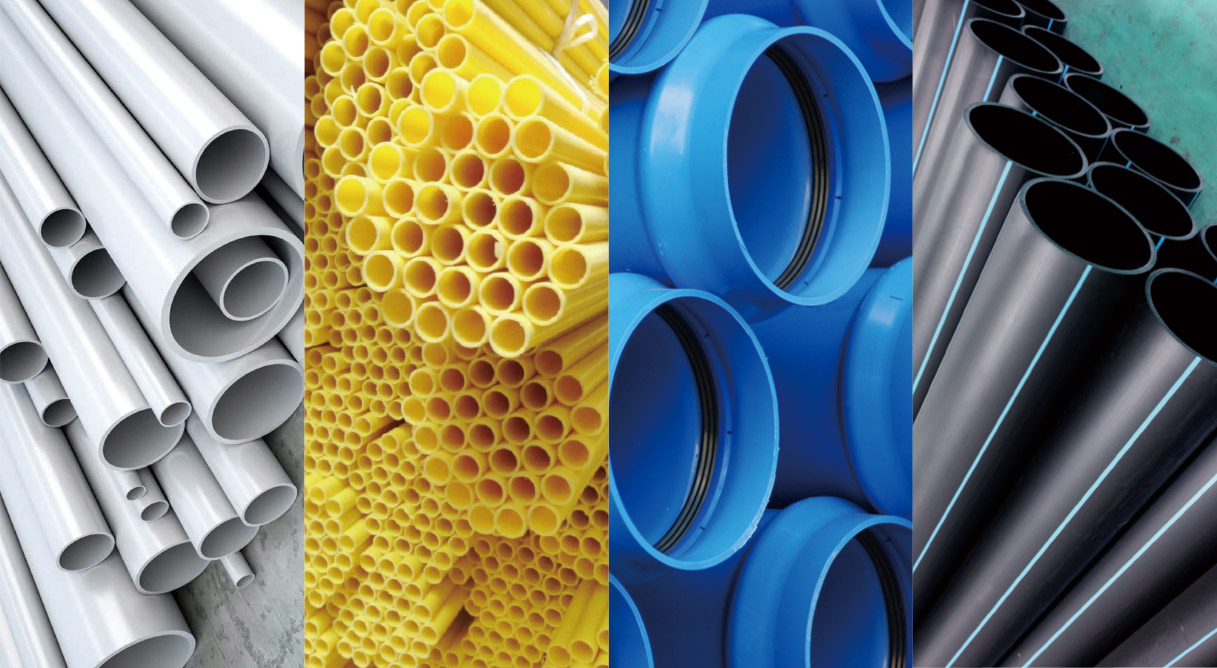
The Role of Plastic Extrusion in the Automotive Market
An overwhelming bulk of parts in modern cars are items of the plastic extrusion procedure. This process has revolutionized the vehicle sector, changing it into an extra reliable, affordable, and versatile manufacturing field. Plastic extrusion is mainly utilized in the manufacturing of numerous automobile components such as bumpers, grills, door panels, and dashboard trim. The process offers an uniform, constant output, allowing suppliers to produce high-volume get rid of great precision go and very little waste. The agility of the extruded plastic parts contributes to the total decrease in automobile weight, improving gas performance. Additionally, the durability and resistance of these components to heat, chilly, and influence enhance the durability of autos. Therefore, plastic extrusion plays a critical duty in vehicle production.
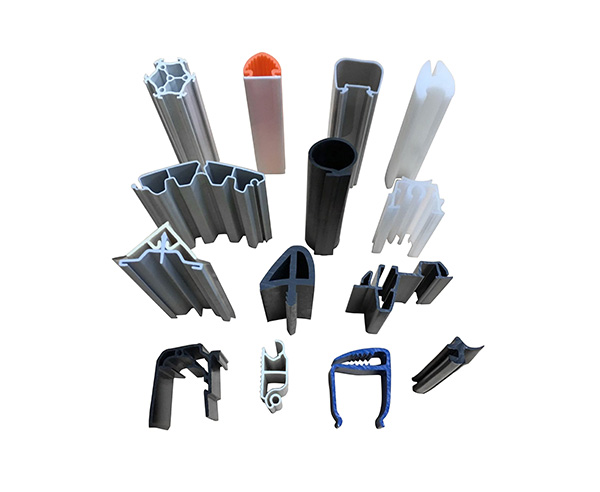
Applications of Plastic Extrusion in Customer Item Manufacturing
Past its considerable influence on the automotive market, plastic extrusion proves similarly effective in the realm of durable goods making. This process is vital in developing a large variety of products, from food product packaging to house home appliances, toys, and also medical devices. The flexibility of plastic extrusion permits suppliers to create and create complicated forms and dimensions with high accuracy and performance. Due to the recyclability of several plastics, extruded components can be recycled, reducing waste and price (plastic extrusion). The flexibility, flexibility, and cost-effectiveness of plastic extrusion make it a favored choice for numerous customer goods manufacturers, contributing dramatically to the market's development and advancement. The ecological ramifications of this extensive use require cautious consideration, a subject to be reviewed further in the subsequent section.
Environmental Effect and Sustainability in Plastic Extrusion
The pervasive use of plastic extrusion in making welcomes examination of its ecological effects. Efficient machinery reduces power usage, while waste monitoring systems recycle scrap pop over to this site plastic, reducing raw material needs. In spite of these renovations, further technology is required to mitigate the environmental footprint of plastic extrusion.
Final thought
To conclude, plastic extrusion plays an important role in modern-day manufacturing, specifically in the automobile and customer products fields. Its flexibility allows for the production of a large range of elements with high precision. Its potential try this web-site for reusing and development of naturally degradable materials offers an encouraging avenue in the direction of lasting methods, therefore resolving ecological worries. Comprehending the fundamentals of this procedure is vital to optimizing its applications and benefits.

The plastic extrusion procedure is thoroughly utilized in numerous sectors due to its cost-effectiveness, flexibility, and performance.
Structure upon the standard understanding of the plastic extrusion procedure, it is required to discover the numerous methods included in this production technique. plastic extrusion. In comparison, sheet extrusion develops big, flat sheets of plastic, which are usually additional refined into items such as food packaging, shower curtains, and car parts.An overwhelming majority of components in modern vehicles are products of the plastic extrusion procedure